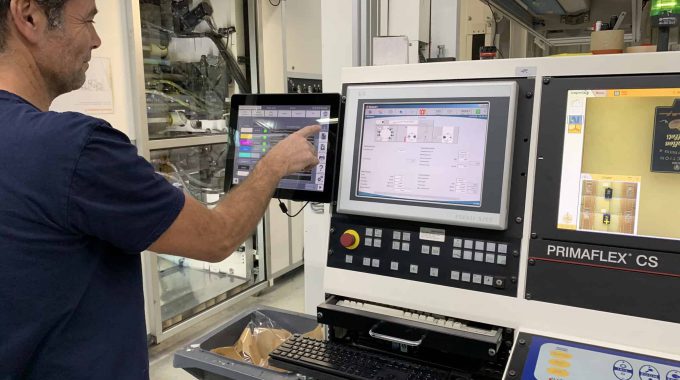
Fleksografik Baskıda Viskozite Standardizasyonu
Flekso ve gravür baskıda en büyük değişkeni kontrol etmek için yeni bir yaklaşım
Giriş
Şirketimizin geçmişinde her türlü viskozite sensörünü uyguladık: dönme, düşen bilye, düşen piston ve akustik dalga. Bu sensörler arasındaki benzerlik, hepsinin bir kapla, bizim durumumuzda 4 mm çıkışlı DIN kabıyla kalibre edilmiş olmasıdır. Bu kendi başına işe yaradı ve daha iyi bir alternatifin bulunmaması nedeniyle DIN kabı 4, flekso ve gravür endüstrisinde standart ölçüm haline geldi. Aralık 2017'de daha iyi bir çözüm ararken şu şirketle iletişime geçtim: Rheonics Kullandığımız, çok hatalı ve yeterince tekrarlanamayan sensörlere alternatif olarak SRV. Ocak 2018'de bu sensörlerden ikisini test etmeye başladık ve Haziran 2018'de CI baskı makinesinin 8 baskı istasyonunun tamamını Rheonics SRV'ler. Geçen yıl birçok test gerçekleştirdik, deneyim ve yeni bilgiler topladık. Bu birimlerle çalışmaya alışkın olduğumuz için, SRV tarafından iletilen birim olan centipoise veya mPaS birimini DIN Kupası 4 saniyeye dönüştürmek için bir formül geliştirdik. Birkaç ay sonra, bu makalede açıklığa kavuşturulacak nedenlerden dolayı DIN Cup ünitelerini kullanmayı tamamen bırakmaya karar verdik.
Mevcut baskı makinesi üretimi, ayarlama açısından son derece hassastır (μm aralığında) ve% 100 kontrol sistemi, aniloks rulolarının ve plaka silindirlerinin tam otomatik baskı ayarı, otomatik kayıt kontrolü ve satır içi spektral renk ölçümü. Bununla birlikte, baskı işlemindeki en büyük değişken olan mürekkebin viskozitesi yine de manuel olarak belirlenen bir birim ile ölçülür! Çoğu durumda, operatörler fincan saniyelerinde düşünmeye alışık oldukları için otomatik viskozite kontrolleri bile bir fincan ile kalibre edilir. Pratikte, viskozite kalibrasyonu genellikle zaman alıcı olduğu veya kapların kirli olduğu veya kullanılamadığı için yapılmaz.
Viskozite, basılı maddenin nihai kalitesinde çok önemli bir parametredir. Viskozite doğru değilse, akış davranışı ve mürekkep katmanı kalınlığı değişir, bu da baskı kalitesinde sorunlara yol açar. Ayrıca, düşük ayarlanmış mürekkep viskozitesi aşırı mürekkep tüketimine neden olabilir.
doğruluk
Her operatör bir çeşit viskozite ölçüm kabı ile çalışmaya alışkındır. Bu ölçümler hiçbir zaman tamamen standartlaştırılmamıştır ve yalnızca büyük bir hata payı (% 5-10) olan nispeten dar bir ölçüm aralığında “güvenilirdir”. Bu hataların bazıları bardağın kendisinden kaynaklanırken, diğerleri operatör becerisinin bir fonksiyonudur. Ölçümler tekrarlanamaz. Viskozite üzerinde güçlü bir etkisi olan sıcaklığın kontrol edilmesi zordur. Haznenin kirlenmesi ve farklı mürekkep yoğunlukları, tükenme hızını etkiler. Bunların tümü, DIN kap ölçümlerinin zayıf tekrarlanabilirliğine ve doğruluğuna katkıda bulunur.
Pratikte, hata marjları% 5-10 kadar yüksek olabilir ki bu büyük bir viskozite bant genişliği demektir. Örneğin, 20 s'lik bir viskoziteye sahip bir mürekkep için,% 5-10 arasındaki bir hata payı, 1 s ile 2 s arasında bir bant genişliği anlamına gelir!
doğruluğu ve tekrarlanabilirliği nasıldır? Rheonics SRV, DIN kap ölçümleriyle karşılaştırılıyor mu?
İşte bir alıntıdır Rheonics SRV spesifikasyon sayfası:
Viskozite Aralığı | 0.4 ila 250,000+ cP |
Viskozite Doğruluğu | Okumanın% 5'i (standart) % 1 ve daha yüksek doğruluk mevcut |
Yeniden üretilebilirlik | Okumanın% 1'inden daha iyi |
Sıcaklık | Pt1000 (DIN EN 60751) |
Proses Akışkan Sıcaklığı | -40 ila 300 ° C (575 ° F) |
Ortam sıcaklığı | -40 ila 150 ° C |
basınç Aralığı | 7,500 bar'a kadar 500 psi'ye kadar |
Sensörün çalışması, sıvıya daldırılan ve rezonansı sıvının viskozitesi tarafından sönümlenen titreşimli bir elemana dayanmaktadır. Rheonics SRV, rezonatörünün tamamen dengeli olması ve doğruluğunun mekanik ortamdan etkilenmemesi açısından diğer titreşimli sensörlerden farklıdır. Aynı zamanda son derece sağlamdır, yani gerektiğinde solvente batırılmış bir bezle silinerek temizlenebilmektedir.
Üreticinin teknik özellikleri, geniş bir ölçüm aralığına ve çok yüksek doğruluğa sahip olduğunu gösteriyor, ancak bu pratikte ne anlama geliyor? 20 kg mürekkebe 25 g solvent ekleyerek doğruluğunu test ettik. Sensör, 0.1 saniyelik fincan ölçüm farkına eşdeğer olan 02 mPaS'lik bir viskozite değişikliği kaydetti! Bu, bu endüstride viskozite ölçümünün daha önce bilinmeyen bir doğruluğu. SRV, algılama elemanına doğru bir sıcaklık ölçümü dahil ettiğinden, bir sonraki bölümde açıklayacağımız gibi, sıcaklığın etkilerini doğru bir şekilde telafi etmek mümkündür.
Kupa ile çalışmanın sadece modası geçmiş değil, aynı zamanda üretken olduğunu da bulduk. Birkaç ay sonra, fincan saniyelerine tamamen dönüşmeyi bıraktık, son olarak baskıdaki son önemli değişken olan viskozite ölçümünü sürecin geri kalanıyla aynı teknolojik seviyeye yükselttik. Sonunda 21. yüzyıla geldik.
Newton dışı davranış, tiksotropi ve sıcaklık dengelemeli viskozite
Doğruluk ve tekrarlanabilirlik nedeniyle Rheonics SRV sensörü sayesinde mürekkeplerin davranışına ilişkin pek çok fikir edindik; bazen beklediğimizden daha fazla. Mürekkep reolojik olarak karmaşık bir ortamdır ve SRV bize, DIN kabıyla gözlemlenemeyen bu karmaşıklığa ilişkin bazı bilgiler verir.
Solvent bazlı mürekkepler Newtonyen olmayan davranış sergiler. Kesme kuvvetinin etkisi altında viskoziteleri değişir. Mürekkep aynı zamanda tiksotropiktir; hareket halindeki bir mürekkepten önemli ölçüde farklı bir viskoziteye sahip sabit bir mürekkeptir. Sabit bir mürekkebin viskozitesi, hareketli bir mürekkebin viskozitesinden %20'ye kadar farklı olabilir! Ayrıca mürekkebin viskozitesi büyük ölçüde sıcaklığa bağlıdır. Mürekkep sıcaklığının ayarlanmadığı baskı makinelerinde, mürekkep sıcaklığı ve dolayısıyla viskozite, ortam sıcaklığındaki değişikliklere ve aynı zamanda baskı makinesinin kendisindeki ısı oluşumuna bağlı olarak büyük ölçüde değişebilir. ile araştırdığımız ilk şeylerden biri Rheonics SRV, mürekkep viskozitesinin sıcaklığa bağımlılığıdır.
Mürekkebin, presimizdeki mürekkep devresine benzer bir hızda sürekli olarak bir devreye pompalandığı ve yavaşça ısıtıldığı kapalı bir akış döngüsünden oluşan bir test düzeneği oluşturduk. Sıcaklık ve viskozite saniyede bir ölçülür ve tipik bir test çalışmasında binden fazla ölçüm noktası verir.
Şekil l'deki grafik, bir dizi farklı mürekkebin (modifiye nitroselüloz mürekkep sarısı, macenta, gümüş ve poliüretan beyazı) 1 ° C sıcaklık aralığında viskozitesinin sıcaklığa bağlılığını göstermektedir. Bu aralıkta viskozite% 20'a kadar değişebilir.
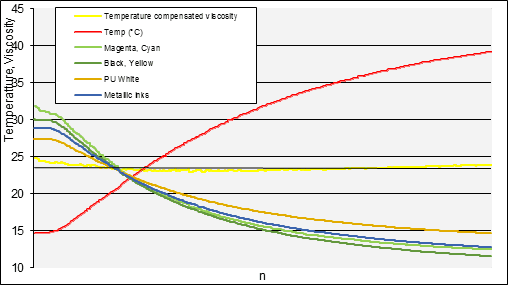
Şekil 1. Mürekkep viskozitesinin sıcaklığa bağımlılığı
Viskozite ölçümünün en önemli kullanımlarından biri, baskı işlemi sırasında solvent kaybını telafi etmek için ne zaman ve ne kadar mürekkep seyreltilmesi gerektiğini belirlemektir. Çözücü buharlaşması mürekkebin pigment yükünü arttırır, bu da düşük baskı kalitesi ve aşırı mürekkep tüketimine neden olur. Bu çözücü kaybı ayrıca mürekkebin viskozitesini de arttırır. Bununla birlikte, viskozite aynı zamanda sıcaklığın güçlü bir fonksiyonu olduğu için, çözücü ilavesinin miktarını ve zamanlamasını belirlemek için sıcaklık ve buharlaşmanın etkileri arasında ayrım yapılması gerekmektedir.
Sıcaklık telafisi olmadan, düşük sıcaklıktaki bir mürekkep, yüksek bir viskozite okuması verir, bu da seyreltmenin gerekli olduğunu gösterir. Bununla birlikte, mürekkebin seyreltilmesi daha düşük bir renk yoğunluğu verecektir, çünkü daha yüksek viskozite, daha yüksek pigment yüklemesine değil, daha düşük sıcaklıktan kaynaklanmaktadır.
Şekil l'dekiler gibi grafikler kullanarak, sıcaklığın viskozite üzerindeki etkisini telafi etmemizi sağlayan, pigment yükünün gerçek bir ölçüsü olan bir "sıcaklık dengelemeli viskozite" ile sonuçlanan bir algoritma geliştirdik. Bu nedenle, buharlaşmayı telafi etmek için çözücü ilavesini kontrol etmek için doğrudan kullanılabilir, çünkü ölçümü etkileyen bir değişken olarak sıcaklığı kaldırır.
Kompanzasyon algoritmamızı kullanarak, tüm sıcaklık aralığında hata sapmasını% 1'e düşürüyoruz. Otomatik viskozite kontrolünde, her mürekkep türü için sıcaklık telafisi seçilebilir. Bu eğriyi kullandığımız hemen hemen her mürekkep için belirledik ve özel algoritmamızı kullanarak sıcaklık dengeleme parametrelerini belirleyerek sonunda pigment yüklemesi ve baskı kalitesi üzerindeki etkisi üzerinde daha sıkı kontrol elde etmemizi sağladık.
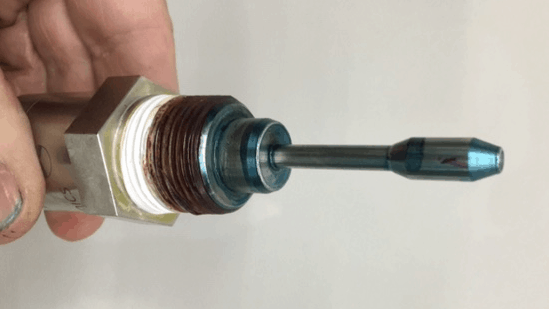
Şekil 2. Camgöbeği mürekkebindeki ölçümden sonra SRV sensörü
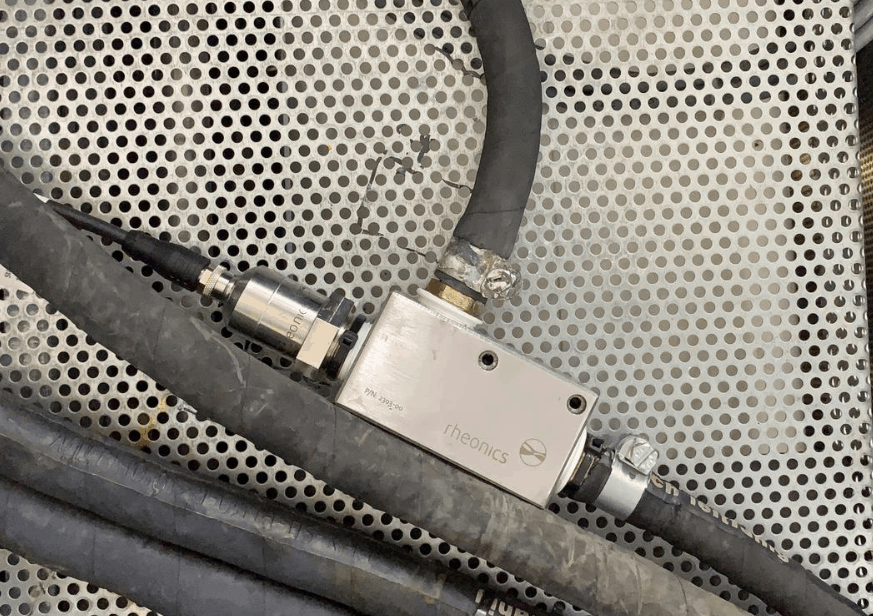
Şekil 3. Mürekkep hattına takılı SRV'yi gösteriyor Rheonics baskı adaptörü
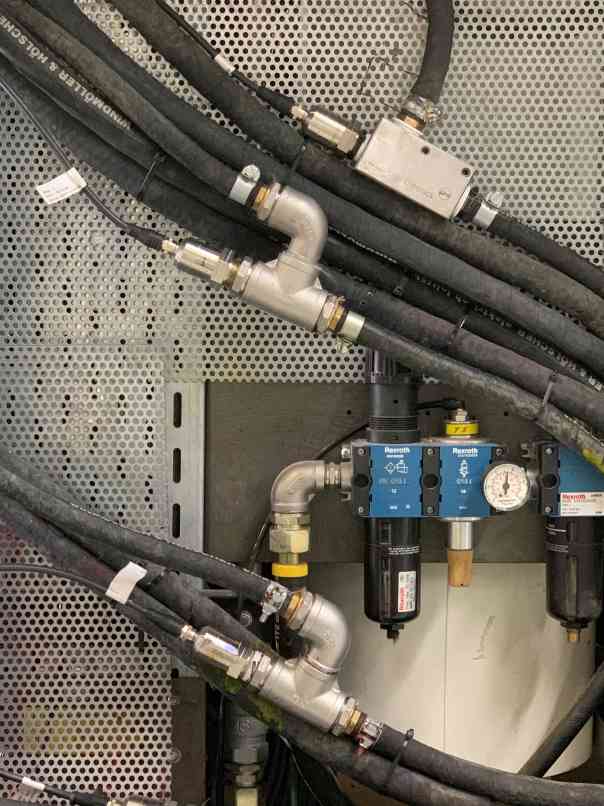
Şekil 4. Adaptör olarak basit boru teesleri kullanan bir pres üzerine kurulu dört SRV
Montaj
Sensör, giriş ve çıkış açıklığına sahip bir konektöre monte edilir ve mürekkep pompası ile doktor odası arasındaki besleme hattına monte edilir. Diyaframlı pompanın makine titreşimleri veya basınç titreşimleri gibi etkilerin sensörün çalışması veya ölçüm doğruluğu üzerinde bir etkisi yoktur.
Sensör bakım gerektirmez - hatların ve doktor odasının her temizlik döngüsü, sensörün otomatik olarak çözücüde yıkandığı için sensörün tekrar temiz olmasını sağlar. Şekil 2'de gösterildiği gibi, sensör üzerinde sadece çok ince bir renk bulanıklığı kalabilir, bu da doğruluğu veya tekrarlanabilirliği üzerinde hiçbir etkisi yoktur. Ve sensörün sağlam yapısı nedeniyle, sensöre zarar verme veya kalibrasyonunu değiştirme tehlikesi olmadan, solventle ıslatılmış bir bezle gerekli herhangi bir temizlik yapılabilir.
Tüm sensörler endüstriyel sınıf kablolarla elektronik ünitelerine ayrı ayrı bağlanır ve bunlar endüstriyel sınıf bir bilgisayarla iletişim kurar. Bilgisayar, solvent dozajı için pnömatik olarak çalıştırılan valfleri kontrol eden bir valf adasını kontrol eder. Sistem, operatör kontrol panelinin yanında, sezgisel kullanıcı arayüzünü çalıştıran bir dokunmatik ekran içerir. Rheonics viskozite kontrol yazılımı Inksight. Kullanıcı arayüzünün oluşturulmasında açık, sezgisel, etkili ve hızlı çalıştırılabilir olması gerektiği açıktı. Arayüz, operatörün tüm istasyonların viskozitesini izleyebileceği bir gösterge tablosu görüntüler. Dokunmaya duyarlı kontroller, operatörün ayrı ayrı istasyonları açmasına veya kapatmasına, otomatik kontrolü etkinleştirmesine ve viskozite sınırlarını ayarlamasına olanak tanır. Ayrı bir istasyon merkezi, zaman içindeki viskoziteyi izleyen ve belirli sensör ve valflerin ayarlanmasına olanak tanıyan bir ekrana geçiş yapar.
Ayrıca, viskozite değişiklikleri çok büyük olduğunda yazılım operatöre haber verir ve sorunu çözmek için doğru düzeltmeyi yaparak yardımcı olur.
Otomatik kontrol, CS-Kontrol
Baskı sırasında solventler sürekli buharlaşır; artan baskı hızı ve artan mürekkep sıcaklığı ile buharlaşma artar. SRV sensörleri, viskozite ve mürekkep sıcaklığının gerçek değerini saniyede bir ölçerek, yazılımın sıcaklık dengelemeli viskoziteyi hesaplamasını sağlar. Bu da kontrolörün sıcaklık dengelemeli viskozitenin istenen tolerans dahilinde olup olmadığını belirlemesini sağlar. Kontrolör, ayar noktasından sapmanın boyutuna bağlı olarak bir miktar solvent ekleyecektir. Baskı sırasında, ayar noktasından sadece% 0.5'lik bir sapma muhafaza etmek mümkündür. Bu kadar ince bir kontrol elde etmek için gerekli olan çok küçük miktarlarda solvent ekleyebilen özel dozaj valfleri kullanılır. Aşağıdaki grafikler, farklı ölçeklerde aynı renktedir ve dikey macenta çizgiler otomatik çözücü dozajını gösterir.
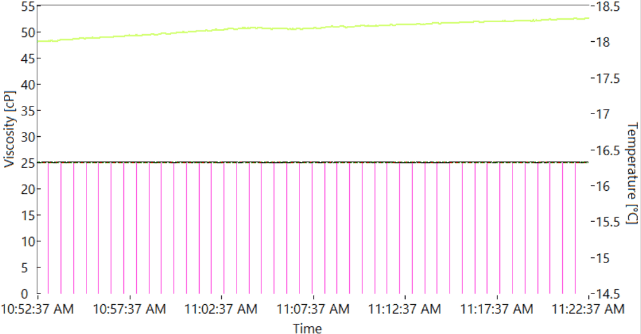
Şekil 5a. Sıcaklık dengelemeli viskozite ve zamana karşı sıcaklık, kaba dikey ölçek
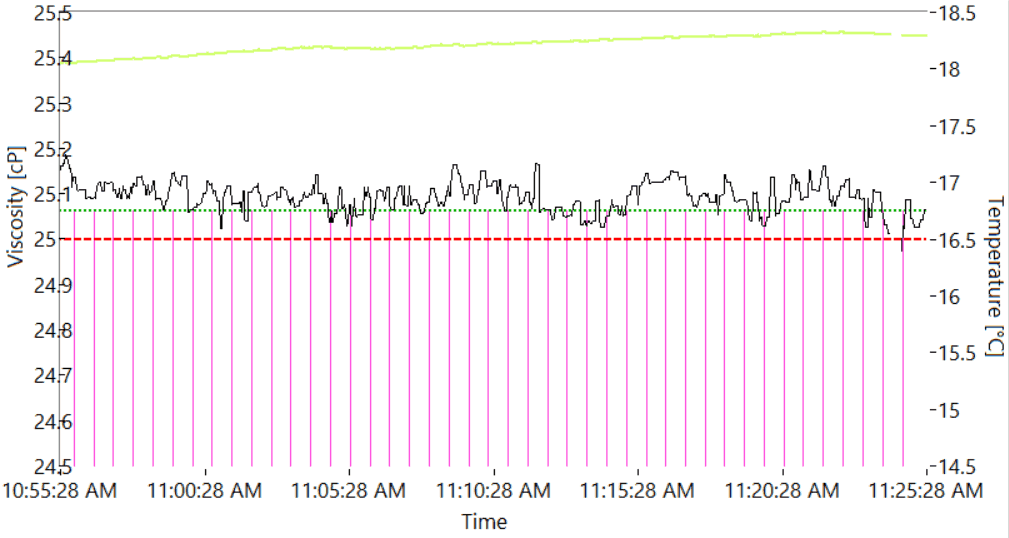
Şekil 6b. Genişletilmiş dikey ölçek ile yukarıdaki ile aynı arsa. Sıcaklık dengelemeli viskozite değişimi 0.2 mPaS'den az
SRV tabanlı kontrol sistemi son derece hassastır, çünkü baskı işlemi sırasında sürekli olarak meydana gelen buharlaşmayı hızlı ve sıklıkla telafi edebilir. Ayar noktasından bu kadar küçük sapmalar elde etmek için, sistem bazen her otuz saniyede bir 10 g kadar az çözücü dozlayacaktır.
Mürekkep kovasına çok yüksek bir viskoziteye sahip bir mürekkep eklenirse, kontrol her bir çözücü dozundaki yanıtı ölçerek derhal tepki verir ve müteakip çözücü dozu buna göre ayarlanır. Sonunda, ayar noktasına çok az aşma ile kademeli olarak ulaşılır. Aşırı hassas kontrolün yanı sıra, mürekkep kovasındaki seviye çok düşük olduğunda, mürekkebi sisteme pompalamak için yeterli olduğunda viskoziteyi sabit tutmak mümkündür.
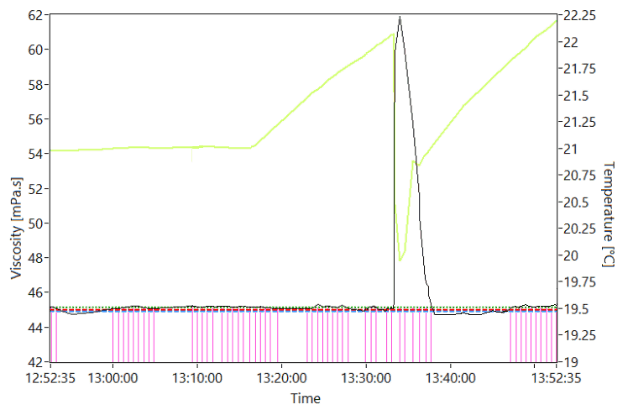
Şekil 6. Sistemin, 21 ° C'de çalışan bir sisteme büyük miktarda soğuk mürekkep eklemesine yanıtı. C. Sıcaklık dengelemeli viskozitenin hızlı toparlanma süresine dikkat edin.
Kalite güvencesi, iyileştirme ve standardizasyon
Deneyimli bir operatör, belirli bir işlemde hangi mürekkep türleri için hangi viskozitenin korunması gerektiğini bilir. Bu, mürekkebin türüne - Pantone renginin yanı sıra, “normal” mürekkeplerden biraz farklı bir davranışa sahip olan metalik ve beyaz mürekkepler tarafından sunulanlar gibi özel zorluklara da bağlıdır. Ve istenen viskozite ayrıca baskının yapıldığı alt tabaka tipine de bağlıdır.
Sorunu ve çözümünü daha iyi anlamak için, mürekkep dilüsyonunun baskı kalitesi ve ölçülen mürekkep viskozitesi üzerindeki etkileri üzerine bir dizi deney yaptık. Bu sonuçlarla, alt tabaka tipi (kağıt, polyester, polietilen, polipropilen) için hangi viskozitelerin korunması gerektiği artık.
İlk denemede 10 kg mürekkep% 10 oranında seyreltildi, pres 200 metre / dakikada çalıştırıldı, polyester film işaretlendi ve pres durduruldu. Mürekkep,% 3 daha fazla çözücü ile seyreltildi, mürekkep, viskozite stabil hale gelene kadar sirküle edildi ve işlem, toplam 15 kez tekrarlandı. Film çıkarıldı ve 15 segmentin hepsi bir spektrofotometre ile ölçüldü ve film segmentlerinin fotoğrafları subjektif görsel değerlendirme için yapıldı.
Aşağıdaki bileşik şekil, bir dizi dilüsyonda baskı kalitesinin görsel görünümünü göstermektedir.
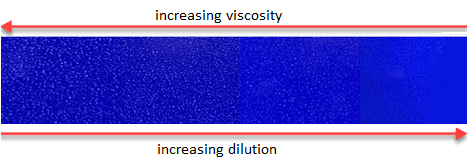
Şekil 7. Mürekkep seyreltmesi ve viskozitesi ile renk yoğunluğu değişimi
En düşük seyreltmede (en yüksek viskozite), çok fazla mürekkep birikiyor ve düzgün şekilde akmıyor. İğne delikleri gelişir ve genel kalite zayıftır. İğne delikleri arasındaki renk oldukça yoğun olmasına rağmen, iğne deliklerinin yüksek yansıtıcılığı nedeniyle ölçülen yoğunluk düşüktür. Seyreltme arttıkça viskozite azalır ve akış artar, ancak pigment yükü azalır ve renk daha açık hale gelir. Her numune spektrofotometre ile ölçüldü ve dijital PMS referansıyla karşılaştırıldı. Aşağıdaki chart ve tablo, seyreltme ve viskozitenin fonksiyonu olarak dE2000'i ve renk yoğunluğunu göstermektedir. Viskozite farkı değerleri, hedef yoğunluk olan numune 6'ya atıfta bulunur.
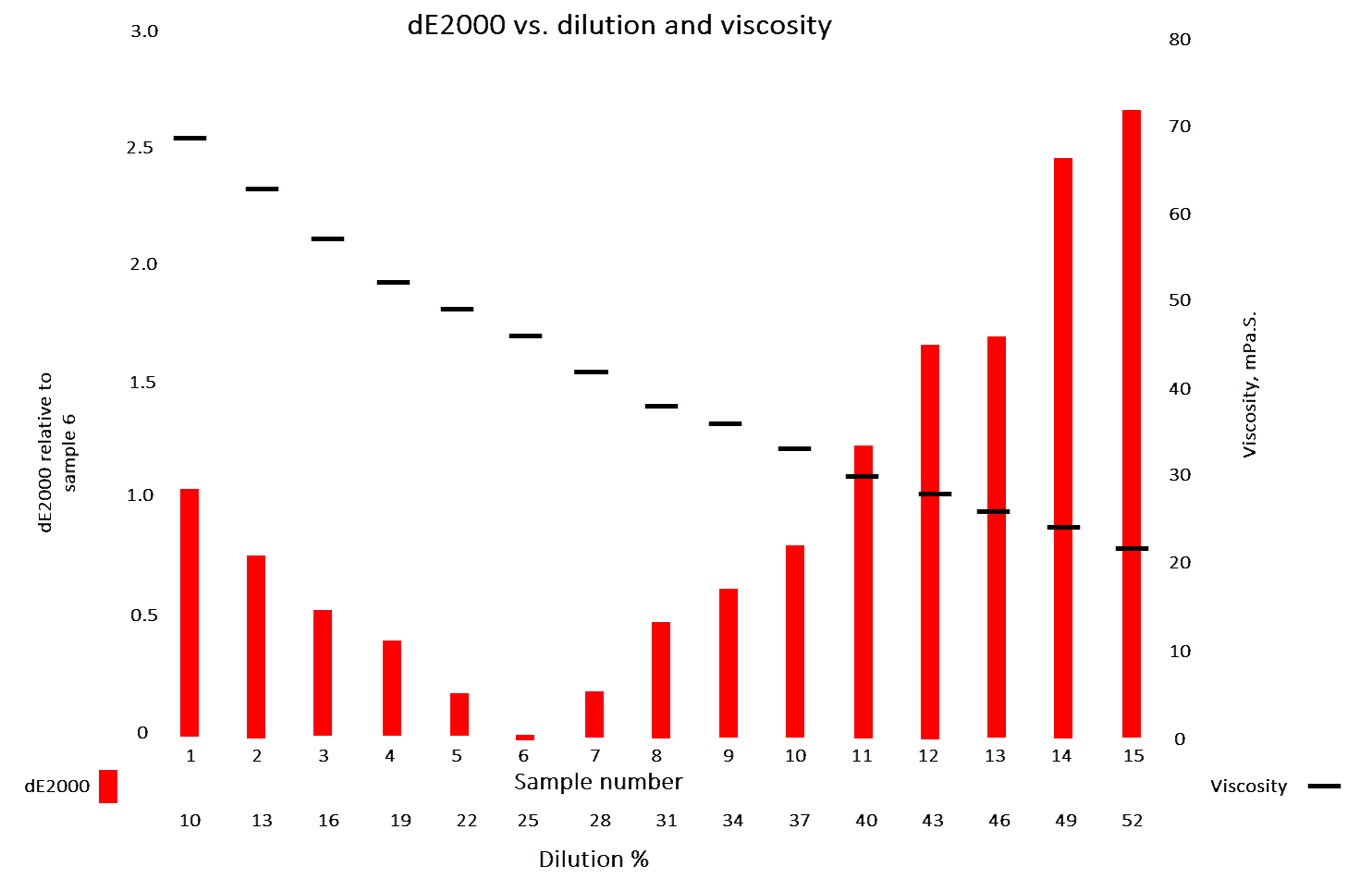
Şekil 8. Mürekkep seyreltmesi ve yoğunluğunun bir fonksiyonu olarak renk yoğunluğu. dE2000 değerleri örnek 6'ya atıfta bulunur
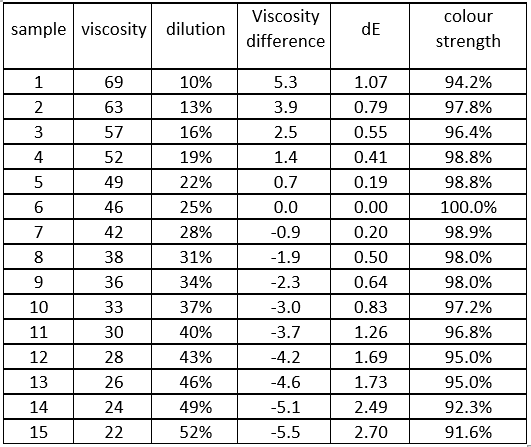
Tablo 1. DE2000'in sayısal değerleri ve seyreltmeye karşı renk mukavemeti. Viskozite farkı Numune 6'ya göredir
Bu deney şunu gösteriyor: Rheonics Sistem, %0.5'lik bir viskozite bant genişliği ile çok hassas bir viskozite kontrolü elde edilebilir. Sistem, yaklaşık her 30 saniyede bir çok küçük miktarlarda solvent dozlayarak, dE değerlerinde çok küçük değişikliklerin elde edilmesini sağlar.
Bu deneyler yapıldığında, alışılmış viskozite bant genişliği, her 0.5-2.2 dakikada bir kontrol edilen viskozite ile ± 5 fincan saniye (yaklaşık ± 10 mPaS) idi. Daha sonra dozlanan çözücü miktarı 0.2 ile 0.5 kg arasındaydı (mürekkep kapsamı, çözücü türü, aniloks hacmi, makine hızı ve sıcaklığa bağlı olarak.
Artık bir Pantone rengi basma sürecini değiştirdik, çünkü yalnızca alt tabaka türü için hangi viskozitelerin korunması gerektiğini bilmekle kalmıyoruz, aynı zamanda bu viskozite konusunda sıkı toleranslara sahip olabiliyoruz. Bazı alt tabakalar, mürekkebin çok fazla "batması" ve böylece yapının görünür hale gelmesi nedeniyle daha yüksek bir viskozite gerektirir, bu da renk gücünde bir azalmaya neden olur; diğer alt tabakalar ise pürüzsüz yüzeyleri ve iyi mürekkep kabulü nedeniyle daha düşük bir viskoziteye ihtiyaç duyar. Kazanılan tecrübe ile Rheonics sensör sayesinde, alt tabaka türü (polietilen, polipropilen, poliamid, polyester, kağıt ve biyolojik olarak parçalanabilir) için hangi viskozitenin korunması gerektiğini tam olarak biliyoruz ve aslında kendimiz için bir standardizasyon belirledik.
İlk baskıda, pantone renginin renk yoğunluğu ölçülür ve operatör, mürekkebin ilgili alt tabaka için doğru viskoziteye sahip olup olmadığını kontrol eder. (Mürekkep genellikle önceden doğru değere getirilmez, çünkü alt tabaka yüzey kalitesi açısından biraz değişebilir, bu nedenle optimum sonuçlar için viskozite ile oynamak için biraz alanımız vardır).
Eski yöntemde, bir renk çok yüksek renk yoğunluğuna sahipse, vernik ve / veya farklı bir aniloks rulo ile azalttık. Şüphe durumunda, viskozite, genellikle ilgili sensörün yeniden kalibrasyonunu gerektiren bir fincan ile kontrol edildi.
Artık mürekkebin ilk sıcaklık dengelemeli viskozitesi için daha güvenilir bir ölçüme sahip olduğumuz için, viskozitesi, mürekkebi doğru değere seyrelterek otomatik olarak ayarlanabilir. Doğru viskozite değerleri korunduğundan, bu, aniloks rulodan baskı plakasına ve son olarak alt tabakaya daha iyi mürekkep transferine yol açar. Aniloks rulosunun kontaminasyonu daha önce fark edilebilir, çünkü belirli bir viskozitede hangi renk gücüne ulaşılması gerektiğini biliyoruz.
Çok yüksek viskozite zayıf transfer ile sonuçlanan donukluk ve “gölgelenme” gibi görsel özelliklere yol açar. Daha hassas bir viskozite nedeniyle, aniloks rulosunun hücresi daha iyi boşaltılır ve mürekkep genellikle daha iyi akar, daha pürüzsüz bir mürekkep tabakası ve artan renk mukavemeti verir. Hız arttıkça, mürekkep aktarımı azalır, ancak mürekkep doğru viskoziteye sahip olduğundan ve en iyi şekilde performans gösterdiğinden, bu varyasyonlar, kap kalibre edilmiş sensörler kullanan önceki yöntemimize kıyasla daha küçüktür.
Son altı ayda geliştik renk kalite ve özellikle dE2000 değerlerinin çok daha küçük sapmalarını koruyabilir. Daha sıkı viskozite kontrolünün bir sonucu, baskı inceleme sisteminin renk gücü sapmalarında çok daha az hata görmesidir. Operatörlerimiz, sensörlerin ve kontrol sisteminin doğru ve tekrarlanabilir değerlerine tamamen güvenmektedir. Bu güven, baskı makinemizin küçük ve büyük işler için mükemmel baskı kalitesi elde etmesine yol açtı. Ek olarak, sensörlerin ne bakımını ne de kalibrasyonunu gerçekleştirdik ve her mürekkep için ilk sıcaklık dengelemeli viskozite parametre ölçümlerimizin ötesinde, viskozite değerlerinin daha fazla standardizasyonuna gerek yoktur. Artık belirli yüzeyler için hangi viskozitelerin korunması gerektiğini biliyoruz. Her yeni siparişi yazdırdıktan sonra, viskozite ayar değerlerini saklıyoruz ve bunları aynı işin tekrar siparişleri için kullanıyoruz.
Bir renk için% 5'lik bir sapma diğeri için geçerli değildir, bir siparişin yazdırılması sırasında dE değerlerini çok daha iyi tutabileceğimizi ve değeri çok daha küçük bir bant genişliği içinde tutabileceğimizi belirtmenin daha iyi olduğunu düşünüyorum. başlangıç değeri.
Öyleyse neden fincan saniyesine dönüştürmüyorsunuz?
Viskozite değerlerini mPaS'tan DIN fincan saniyelerine dönüştürmek için formüller mevcut olsa da, fincan saniyelerinin bırakılmasının çeşitli avantajları olduğunu bulduk.
Her şeyden önce, viskozite hakkında düşünme şeklimizi değiştirdi. Kupa saniyesi açısından düşündüğümüz sürece, viskozite üzerinde sıkı bir kontrol tutmak imkansız bir görev gibi görünüyordu. Beklentilerimiz önceki deneyimlerimizle sınırlıydı, bu yüzden çıtayı, ulaşılabilir olduğunu bildiğimiz baskı kalitesine ulaşmak için gerekenden daha düşük ayarladık.
Ayrıca, fincan saniye cinsinden düşünmek, bir fincan kapmamızı ve o zamanlar bilmediğimiz bu yeni sensörlerin doğruluğunu kontrol etmemizi sağladı. Ancak, sensörlerin doğruluğunu çok daha az tekrarlanabilir bir yöntemle kontrol etmek, sensörlerin kendilerinin tekrarlanamayacağı konusunda yanlış bir izlenim verebilir! Sadece yeni sensör sistemini kullanarak gerçek baskı sonuçlarını alışkın olduğumuzla karşılaştırdığımızda, yeni, tanıdık birimlerde düşünmenin gerçek değerini gördük. “Küçük düşünmemizi”, başka türlü görünmeyen viskozitede küçük varyasyonları görebilmemizi sağladı. Dahası, viskozitemizi nihai ürünümüzün kalitesi üzerinde doğrudan olumlu etkisi olan daha sıkı kontrol altına almamıza izin veriyor, sonuçta ana hedefimiz.
Baskı hızları arttıkça ve kar marjları daraldıkça “ilk seferde doğru yapmak” çok daha önemli hale geliyor. Başlangıç viskozite ayarındaki bir hata, kısa sürede binlerce metre atık üretilmesine neden olabilir. İle Rheonics SRV sistemi sayesinde, renk kalitesini artırırken ve israfı azaltırken baskı sürecimizi kolaylaştırabildik.
Bu dizinin bir sonraki makalesinde
Bu makalede viskozite denetiminin temel zorluğuna odaklandık.oring ve kontrol, baskı kalitesi ve mürekkep ekonomisi açısından sıkı kontrolün faydasını gösteriyor. Bir sonraki yazımızda pres operatörünün bu kaliteyi minimum müdahale ile yakalayıp korumasını sağlayan kontrol sistemine daha yakından bakacağız. Sistem, Rheonics Yazdırma Çözümü (RPS), ölçülen viskoziteye göre solvent seyreltmesini doğrudan kontrol eden bir proses bilgisayarı ve valf kontrolünü içeren bir kontrol kutusundan oluşur. RPS, SRV sensörlerinin izleme işlemini gerçekleştirdiği 10 adede kadar baskı istasyonunu barındırabiliroring. RPS donanımı, ölçülen viskoziteye dayalı olarak gerekli seyreltmeyi tahmin eden ve istenen viskoziteyi ayarlamak için basit ve sezgisel bir kullanıcı arayüzü tarafından kontrol edilen gelişmiş bir yazılım sistemi tarafından desteklenir.
Ayrıca, viskozitesi çok sıcaklığa duyarlı olan ve viskozitesi en iyi termal kontrollerle kontrol edilen UV mürekkepleri gibi özel mürekkeplerin viskozite kontrolü sorununu da ele alacağız.